Flowchart |
Feedback |
Six Sigma Conference |
Job opportunities for Lean SSGBs/SSBBs
Practical Experiments
|
More and more jobs are in Analytics, Big data & Cloud
* What
is Six Sigma? 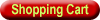
Six Sigma is a rigorous and disciplined methodology that uses data
and statistical analysis to measure and improve a company's operational
performance by identifying and eliminating "defects" in manufacturing
and service-related processes. Commonly defined as 3.4 defects per
million opportunities. Six Sigma can be defined and understood at three
distinct levels: metric, methodology and philosophy.
Six Sigma is a customer focused, data driven methodology for
achieving real break through success in business. Six Sigma is a
comprehensive and flexible system and can be applied to reduce defects,
improve designs and process efficiencies.
Why 3Sigma
Performance Level (99.73%) is not enough?
A three Sigma level company is not good enough, because a 3Sigma
level performance means,
* 200,00 lost articles of mail per hour.
* No electricity for almost 7 hours, each month.
* 2 short or long landings at major airports, each day.
* 200,000 wrong drug prescriptions each year.
* Unsafe drinking water almost 15 minutes each day.
* 5000 wrong surgical operations per week.
(The above information is based on a survey conducted in US.)
Now, can anyone afford to stop at 3Sigma level performance? If a
company performs even at 3Sigma level, (that is 99.73% result fall with
in the control limits) the above defects are possible. Because of the
above cited huge loses, generally many companies go for Six Sigma
Implementation Programs/Certification.
Why you need to
do Six Sigma?
Six Sigma can cut waste and save money. Consider how much money
could be saved by eliminating potential defects and the resulting scrap
and warranty returns. Time and money may be wasted in corrective
actions and delays. Also consider the image those results from product
failures for the customer. In order to determine the waste, you need to
understand what adds value to your product and what does not.
One way to know how good you are doing is to compare your operation
to similar ones elsewhere, as a benchmark. If there are similar
operations in your organization, then bench marking will be easier.
Six Sigma Costs
and Savings:
One cannot expect to significantly reduce costs and increase sales
using Six Sigma without investing in training, organizational
infrastructure and culture evolution. It is sure you can reduce costs
and increase sales in a localized area of a business using the Six
Sigma quality methodology. For Example,
"Motorola adopted Six Sigma in1987. In 1988, Motorola won its first
Baldridge Award."
"Companies of all types and sizes are in the midst of a quality
revolution. GE saved $12 billion over five years and
added $1 to its earnings per share. Honeywell (AlliedSignal)
recorded more than $800 million in savings."
"GE produces annual benefits of over $2.5 billion across the
organization from Six Sigma."
"Motorola reduced manufacturing costs by $1.4 billion from
1987-1994."
"Six Sigma reportedly saved Motorola $15 billion over the last 11
years."
Who should attend?
CEOs, Presidents, Project Managers, Team leaders/Members, Field
Staff Members, Project Engineers, Design Engineers, Project Leaders and
Administrators, Industrial Engineers, Program Managers, Manufacturing
Engineers, Project Coordinators, Operating Managers, Functional
Managers, Information Technology Professionals, Software Developers,
Quality & Testing Engineers, Sales & Marketing professionals,
Civil/Mechanical/Electrical engineers, Procurement specialists, Event
mangers, R&D Managers, others involved directly or indirectly with
Project Management, Quality assurance managers, BPO team leaders, and
Executive leadership from Finance, Training, Communications, Human
Resources and Quality who are interested in gaining a better
understanding of manufacturing processes and reducing process
variability in order to improve business success.
This includes:
* Individuals who desire to enhance their professional development
with the skills necessary to support Six Sigma
projects.
* Employees of companies that have deployed Six Sigma, who work
with Black Belts, or who lead their own
improvement projects. Companies that want to expand
training across a wide range of employees to reduce
costs and improve performance.
Course Structure
(ONLINE):
All candidates will be awarded IIPMs Lean Six Sigma Black Belt
certificate (LSSBB) once a candidate meets the
following criteria:
1. Studies at least 50 hours online and answers exercises given at
the end of the chapters.
2. Passes the IIPMs online Six Sigma Black Belt Exam.
3. Submits any quality improvement (Internal / External) project
using relevant quality tools at unit level or
function level (Green Belt Level). Necessary
sample Green Belt project templates and necessary guidance in GB
project completion are provided by IIPM faculty a
part of the Black Belt course.
Candidates who fulfills the above criteria will be couriered the
original Six Sigma Black Belt Certificate free of cost anywhere in the
world.
Access to the participants to the online resources is available for
6 months including the quality improvement / Green Belt project
completion time. The course is supplied with an end of the course
evaluation test of what was learnt and the participants will be
supported with excellent templates wherever required.
All online participants who are PMPs will earn 40 PDUs Certificate
towards their CCR once they have completed 40 hours of online study
through this PMI approved course.
Salient features
of LSSBB course:
* Hypothesis
Testing – Additional practical examples.
* Statistical process control – Details.
* Sample size calculations.
* DOE (Design of Experiments) in detail with a practical exercise.
* Measurement System Analysis – Gage R&R studies.
* Learn how to deal with non-normal data.
* Hands on practice on Minitab software.
* There are excellent career growth opportunities for Black Belts
which span across functions and industries.
Course fee for
Lean Six Sigma BLACK BELT Certification - ONLINE COURSE:
* Black Belt Certificate Only - US $ 700 only
To See a Sample Certificate.
Click Here
PDUs Offered:
Earn 40 PDUs (PMI Approved) - Click here to see PMI Approval.
Lean Six Sigma
BLACK BELT Final Exam:
An open book paper based exam will be conducted on the final day of
the course. The exam is conducted to measure the knowledge gained by
the participants and to demonstrate the added confidence level out of
this course. Candidates have to secure 50% of marks to issue the Lean
Six Sigma BLACK BELT certificate.
Six Sigma BLACK BELT Project Details:
Please note that the projects for improvement can be from your own
company (or) any other company. The projects can address the entire
company are small portion (or) part (or) division (or) a small process
of a business unit within the company. The candidates can also suggest
project titles from their company for the faculty / instructors /
suggestions (or) they can choose any one of the projects available at
IIPM. IIPM will facilitate the collection of data and extend support
staff services for the project period.
Lean Six Sigma
Projects Guided by IIPM:
1. Case management in Microsoft, Sutherland – A Case
study - BPO Industry.
2. Reducing Turn Around Time (TAT) of Production Support Request in
Cambridge Solution – A Case study -
Manufacturing Industry.
3. Reduction of OLA Deviation in CVS processing in SIFY – A Case
study - Software Industry.
4. Reduction in Manufacturing of Flanges Production Turn Around
Time (TAT)-A Case study-
Construction /Fabrication Industry.
Some example
projects are below.
1) Registration process improvement.
2) Defects and improvements in Training.
3) Defects and improvement in online training.
4) Customer Call registration Improvement.
5) Training course-ware quality improvement.
6) Admin and maintenance expenses improvement.
7) MARKETING EXPENSES IMPROVEMENT: RETURN ON INVESTMENT (ROI).
The participants can identify projects in their own organization
and implement the DMAIC methodology and show significant improvement in
organization. The Students shall review the projects with IIPM on
monthly basis. Any questions clarifications can be discussed during the
review. Sample project is available for all Online/Classroom registered
participants.
Practical
Hands-on Six Sigma Experiments
The following practical hands-on experiments will be conducted and
guided by Mr. Ari to reinforce the theoretical learning into practical
application of six sigma concepts.
1) Mistake proofing (Poke Yoke)
2) Design of Experiments (DOE)
3) Construction of Normal/Binomial Probability curve using a game
of chance
4) Accuracy Vs Precision
5) 5S
6) Reproducibility & Repeatability (Gage R&R)
7) Failure Mode & Effects Analysis (FMEA)
Recent job opportunities for Lean Six Sigma Green
Belts/Black Belts
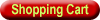
Lean SIX SIGMA BLACK BELT ONLINE COURSE CONTENTS
PART: I-Six Sigma Maturity
Assessment
PART :II-Six Sigma Introduction
Six Sigma : A Primer
Six Sigma Black Belt Body of Knowledge
Six Sigma Black Belt - Lessons
PART :III- Preparing For Deployment
Chapter 1: Enterprise-wide Deployment [9 Questions]
Chapter 2: Business Process Management [9 Questions]
Chapter 3: Project Management [16 Questions]
PART IV: DMAIC Methodology
Chapter 1: DEFINE STAGE [15 Questions]
1.Project Scope
2.Metrics
3.Problem Statement
Chapter 2: MEASURE STAGE [26 Questions]
1.Process Analysis and Documentation
2.Probability and Statistics
3.Collecting and Summarizing Data
4.Properties and Applications of Probability Distribution
5.Measurement Systems.
6 .Analyzing Process Capability
Chapter 3: ANALYZE STAGE [24 Questions]
1.Exploratory Data Analysis
2.Hypothesis Testing
Chapter 4: IMPROVE STAGE [23 Questions]
1.Design of Experiment (DOE)
2.Response Surface Methodology (RSM)
3.Evolutionary Operations. (EVOP)
Chapter 5: CONTROL STAGE [21 Questions]
1.Statistical Process Control
2.Advanced Statistical Process Control
3.Lean Tools for Control
4.Measurement System Re-Analysis
PART: V - LEAN CONCEPTS [7 Questions]
Chapter 1: Lean Enterprise
Chapter 2: Design for Six Sigma (DFSS)
Part: VI - Minitab Application
PART: VI - Case Studies
Case Study 1: Website Response Time
Case Study 2: Reducing Helpdesk Turnaround Time
Case Study 3: Account Withdrawal Accuracy
PART: VII - Practice E-Cards (Flash Cards)
Flash Cards- E-cards- about 100 excellent E-cards for practicing /
exam preparation will be given to each candidate
PART: VIII - Templates
1. Sigma Level to DPMO Conversion (.doc)
2. Estimating Sigma Using Long-Term DPMO (.doc)
3. Random Number Generators (.doc)
4. Six Sigma Table (.doc)
5. Difference between Six Sigma & TQM (.doc)
|
|
|